Spiral-Wound Filters A Lynchpin For Ultrafiltration And Microfiltration Applications
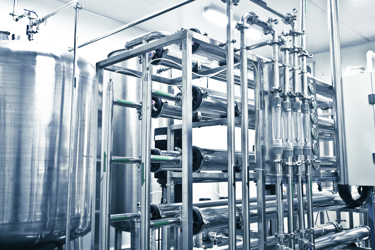
Clean water is essential for a wide variety of processes, but its dwindling availability and rising costs are prompting industrial users to incorporate technologies that promote recovery and reuse.
Spiral-wound filters are beneficial for these applications because the design enables high volumes of permeable membrane to be packed into a confined space. As a result, the filters can be highly effective and economical for removing contaminants. However, the compact nature of their design makes them susceptible to accumulations that reduce their lifespan.
The good news is that new developments in single-layer membrane technology are allowing filter elements to generate higher flux rates and cleaner permeate while reducing the tendency for fouling.
Water Online spoke with Andrew Flowers, PPG research and development engineer, about the challenges facing industrial users and the potential for improved filtration to help achieve their long-term goals.
How do the new PPG membranes enhance filter elements?
By combining a polymer matrix with an inorganic filler — kind of a hybrid between a polymeric and ceramic filter — it offers the best of both worlds: a durable, yet affordable solution. This is integral to separating oil from water and promoting a higher flux rate. We worked on, and continue to work on, spiral-wound designs that leverage the high flux membrane to increase the flux rate of the element itself.
Why is this important in many industrial settings?
Disposal of oily and greasy water can be tricky as well as costly. Industrial users typically can’t just run it down the municipal (wastewater) lines, so it needs to be treated. In some cases, these companies generate massive amounts of wastewater from their processes, and municipalities are also requiring them to reduce the volume. They’re left with two choices: recover and recycle the water to a quality level where it can be reused, or cart it away by truck for disposal.
Another factor that comes into play is when clean water is not readily available — a growing problem across the globe.
When it comes to oils and other solvents, you want to be able to capture enough during the filtration process that the permeate stream meets a targeted water quality at an economic rate. This is governed by how much clean water per unit time you can generate per filter, but it is the membrane’s flux rate that has the ability to drive the economics.
When you talk about the economics of filtration, how does that translate into lifecycle considerations?
We’ve installed PPG filters into systems and the result has been equal or longer life in all cases compared to the incumbent filters, with no changes to the equipment whatsoever. This includes more than 100,000 hours of run time in PPG’s electrocoat application alone. That can only improve as the systems are optimized or new systems are built. Most of the customers we have today installed our technology because it saves them money.
Are there any additional benefits to PPG filters?
A significant factor is their ability to “back pulse” — essentially short bursts of backwashing — which allows spiral-wound filter configurations to be used for very difficult to treat (high-solid or high-particulate) applications where only tubular membranes could be used in the past. This has a sizeable impact on reducing the filtration system footprint and cost.
Also, in situations where water needs to be purified to a level that requires reverse osmosis — which is very sensitive to trace amounts of oils and greases — there’s been a significant benefit to installing the PPG filters ahead of the reverse osmosis (RO) system to protect it.
How does PPG enable simple, drop-in replacement of existing filter elements?
They’re industry-standard configurations and sizes. It’s an easy swap-out because there isn’t a need to change plumbing lines or buy new equipment. The only thing you might have to do is change adapters.
What’s the most notable new advancement from PPG?
PPG is a coatings and specialty materials company, unlike most other membrane providers, and we’ve leveraged our global coatings expertise to introduce an anti-fouling coating in late 2019. This is a permanent coating that is chemically adhered to the membrane. The proprietary technology, available as an option, is intended for extremely difficult oil-laden streams that were previously almost impossible to treat.